黑斑问题一直是电池片EL不良的前三项问题,黑斑的种类多,从异常的产生来讲可以分为两类,一类为偶然工艺原因,此类主要有不规则、不定期的特点,另一类是规则出现,特征性强。本文主要针对电池片的EL测试规则黑斑问题展开分析并提出一些意见。
EL测试原理
EL测试仪是通过对电池片通入1-40mA的正向电流,作用于扩散结两边,电能把处于基态的原子进行激发,使其处于激发态,处于激发态的原子不稳定,进行自发辐射。通过滤波片的作用及底片的曝光程度来了解在自发辐射中本征跃迁的情况,通过少子寿命、密度与光强间的关系,从底片的曝光程度,来判断硅片中是否存在缺陷。
由于晶硅太阳电池中少子的扩散长度远远大于势垒宽度,电子和空穴通过势垒区时因复合而消失的几率很小。在正向偏置电压下,p-n结势垒区和扩散区注入了少数载流子,这些非平衡少数载流子不断与多数载流子复合而发光。
EL黑斑产生的原因
EL测试的图像亮度与电池片的少子寿命(或少子扩散长度)与电流密度成正比,在有缺陷的区域,其少子扩散长度低,发光强度弱。由于电池片中有缺陷区域没有发出红外光,故在EL图像中呈现“黑斑”。
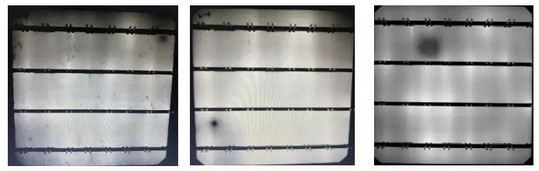
类型1:特别黑的小点,位置随机不固定;
类型2:密集型黑点,黑点区域广,一般满片均匀分布;
类型3:大黑斑,颜色灰色、深灰,位置比较规则;
以下将对上述几种进行简要分析:
1、效率
该类异常黑斑,在电性能无明显体现在FF、Isc、Voc、Rsh上。(说明该类异常片主要非来自正面的影响,切未破坏结区,影响载流子的输运。)
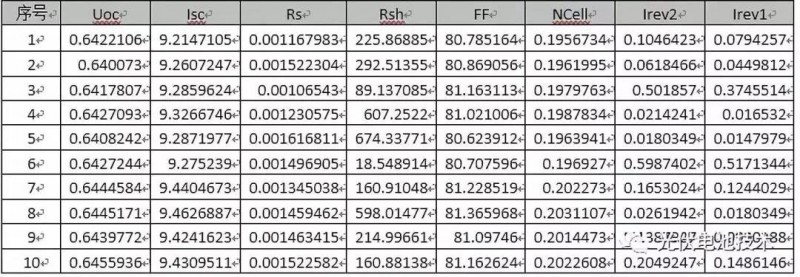
2、量子效率测试
量子效率是用来表征光电转换器件(图像传感器,硅光电池等等)效率的重要指标。太阳能电池的量子效率是指太阳能电池的电荷载流子数目与照射在太阳能电池表面一定能量的光子数目的比率,因此太阳能电池量子效率与太阳能电池对照射在太阳能电池表面的各个波长的光的响应有关。
以下为不同黑斑片对应外量子效率图:
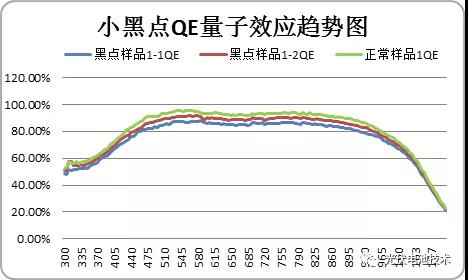
图1
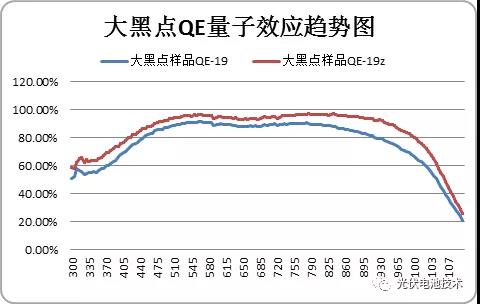
图2
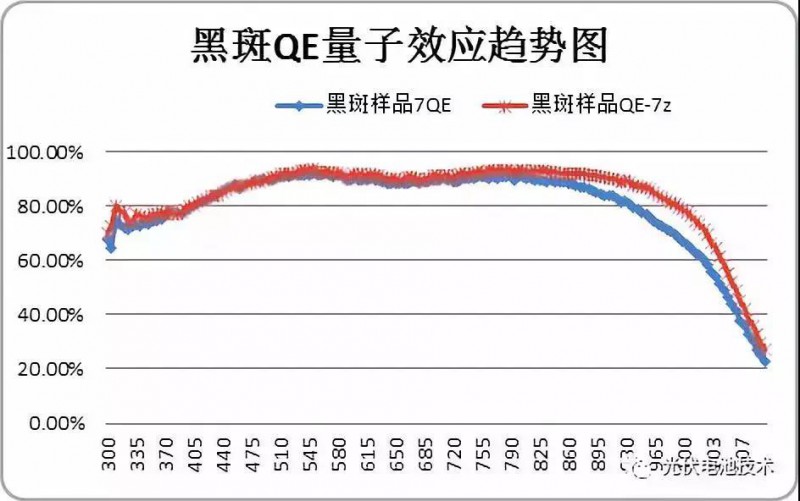
图3
如图1-3,正常单晶电池片和黑斑电池片的量子效应随波长的变化趋势大致相同,说明与硅片的质量关系较小。
图2图3中显示中长波正常区域比黑斑区域量子效率高,波长较长的波是被电池主体吸收的,迁移过程及背面表会产生复合,而量子效率与电池片的活性层对光子利用率以及光的反射、透射有关,实验中黑斑区域和正常区域选自同一片电池片,可以认为它的扩散深度、减反膜相同,因而推断此异常是电池清洗过程残留杂质或背场钝化的问题。
图1整个波段没有明显差异,只是中波段正常区域比黑斑区域量子效率略高,工艺过程不是问题,问题主要是整个生产过程杂质颗粒对电池半成品的污染所致。
3、成份元素分析,测试仪器:ICP-MS
测试原理:采用激光烧蚀的方法,对电池片正常区域和异常区域的分别测试成分含量。酸洗过的电池片制成片状小样置于样品台上,样品表面处激光束聚焦点上。激光器激光轰击,在样品上产生小深坑,消耗样品让等离子体气流过样品表面,再经一导管导入等离子炬,样品在焰炬中电离,通过质谱仪可以对样品微小区域进行分析。
为了降低生产过程及硅片对实验的干扰,每类正常样品和黑斑样品均取自同一张电池片。
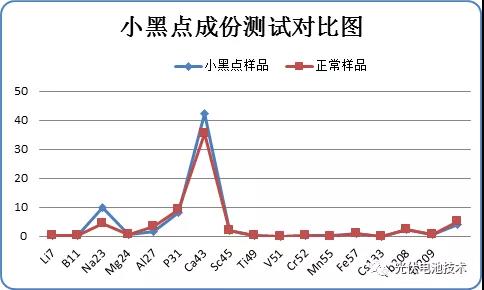
图4 小黑点成分测试图
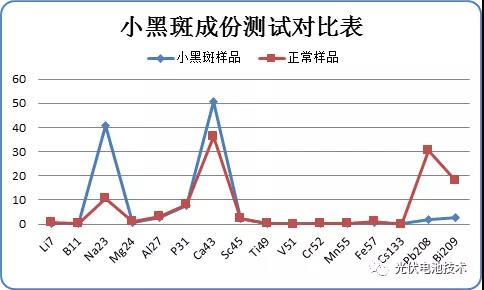
图5 小黑斑成份测试图
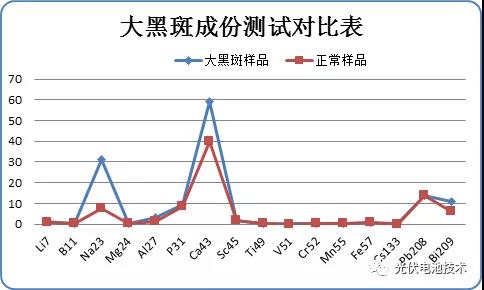
图6 大黑斑成份测试图
如图4小黑点类,正常样品和黑点样品元素含量差异没有明显变化,唯有 Na原子和Ca原子略有差异,黑点样品比正常样品Na含量高132%倍、Ca含量高19.8%倍。
图5小黑斑类,小黑斑样品比正常样品Na含量高283%倍、Ca含量高38.7%倍。
图6大黑斑类,黑斑样品比正常样品Na含量高317%倍、Ca含量高49.4%倍。
从数据来推断图5、图6在黑斑区域杂质元素含量明显高,形成了较强的复合中心,而我们的测试样品是经过混合酸去除了电极和背场,在电池生产含Na和Ca元素的是酸液,而只有刻蚀和制绒两个工序涉及,刻蚀工序酸洗的是电池片背面,我们测试是正面烧蚀厚度约15μm,因此制绒酸液残留的可能性较大,图4在小黑点区域略高,粉尘颗粒在过程中污染表面的可能性较大。
4、P+层少子寿命、方阻测试
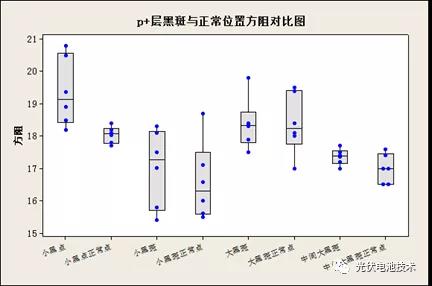
图7 P+层方阻对比图
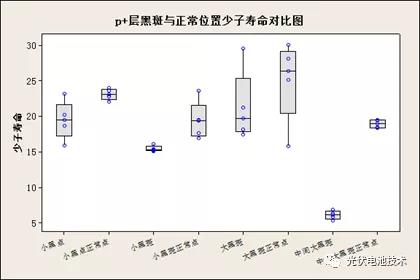
图8 P+层少子寿命对比图
黑斑电池片正常区域和异常区域P+层方阻变化不大,说明背场烧结工艺正常,在少子寿命的表现上只有中间大黑斑明显偏低,而少子寿命偏低主要是受杂质复合影响。因此推论黑点黑斑电池片并非烧结工序所致。
结论:
在这里说明一下,该类黑斑主要针对于未见明显影响到效率的且外观不可见的类型。
笔者在国投在职期间。通过与各组负责人跟踪各道测试片,扩散首尾片,以及玛雅背钝化掉渣外观明显的片子等,验证到以下内容:
1、黑斑非刻蚀、制绒清洗不足导致。仍怀疑清洗后Q-time时间长仍可能导致(针对部分高效不达标的车间,且无氮气柜及封闭式传输小车的公司)以上通过改善循环,增加后HCL补加,初配,降低NAOH耗量对比批量数据。
2、黑斑形成与玛雅掉的碎渣无关。(跟踪验证该类片大一些的仅会形成淡的小灰斑点,不影响电池片EL)
3、跟踪玛雅维护前后发现该类异常片处于半爆发状态,锁定主要来源于背钝化。(经与其他公司沟通也有该类似问题存在,维护前后相差较大)
4、元素分析显示NA离子等,可以考虑将制绒和刻蚀碱改用KOH。这里不作过多说明。
5、控制各制程Q-TIME时间,尤其是湿法工序后,不要超1.5H。平时需放久一些可以考虑使用保鲜膜进行包裹或放置氮气柜。
6、热工序因环境温度关系洁净度需跟加控制好。这里建议一些不达标的公司可洒水。将一些粒子吸附到地面,避免与硅片接触。
7、扩散档片定期跟换。
8、建议将背钝化设备设计隔离间,方便维护,保护其他相邻道工序不受影响。
9、石墨舟清洗需要干净,不干净的石墨舟除了会导致舟印外还会有一些与舟贴合的地方留下小斑点。
10、对于固定位置的黑斑,可以根据硅片加工流程,将各道工装夹具进行点检,并画出相应接触点的图,方便日后的排查。