毫无疑问,HJT是当下最被光伏业内寄予厚望的下一代电池技术路线。单晶PERC背钝化技术,量产效率在22.5%左右,已逼近其结构的工艺极限效率(23.5%左右),业内期待HJT异质结电池能够接棒,扛起下一代高效电池的大旗。其研发效率已经超过25%,批量生产效率达到24.5%,产业化条件基本成熟,预计在未来一两年内将迎来爆发性发展和增长。
但是要实现异质结电池产业化,目前仍存在几大 “痛点”主要包括:
N型硅片成本高
银浆耗量高
组件封装损失等问题。
“低生产成本、高效率、长效”一直被视为光伏电池的“不可能三角”,但这种局面在近期有望被打破。
另一条技术路线MWT向HJT伸出了橄榄枝。
近日,针对行业不断的合作期盼,日托光伏对外宣布:“鉴于MWT技术与HJT可完美结合,公司秉持开放态度,愿与业内HJT企业开展技术合作,共同推进HJT技术的快速发展。”
日托光伏总裁张凤鸣博士表示:“高效背接触MWT技术可完美解决HJT技术的难点,为实现异质结电池产业化快速推进带来了新动力。背接触MWT技术和HJT异质结技术的结合,可以实现超高效MWT+HJT电池的规模化量产,不仅进一步提升电池转效率,也为降低单瓦成本打开新的空间。”
几乎所有主流电池和组件企业和及研究机构都曾MWT电池这项技术都有涉猎,但到现在为止,日托光伏成为行业内唯一一家实现MWT组件GW级量产的企业。据张凤鸣介绍,MWT既是电池工艺,又是组件工艺,它本质是一个技术平台,能够承载PERC、TOPCon、HJT等技术,与其完美叠加。
““MWT+HJT”,是业内最先进的组件封装工艺和电池工艺的完美结合。”张凤鸣表示,“具备降本、省银、更高效等多项优势。”
高效率,MWT+HJT双效叠加
近日,日托光伏推出了MWT+HJT产品解决方案——C-Pro系列。
据日托光伏研发人员介绍,C-Pro系列产品为N型单晶硅高效电池,一方面在技术端融合了MWT+HJT两大先进技术的效率优势,电池平均量产效率达到25%以上,另一方面产品端还可同时实现超大尺寸(G12硅片:210mm*210mm)和超薄(<120μm)硅片电池的制造技术,这样单片电池功率达到11W以上,较现有常规高效PERC电池转换效率提升2.5%(绝对值),单片功率提升10%以上,同时生产成本可以做到更低,对现有常规高效PERC电池形成替代性优势。此外,相比较常规HJT电池,MWT+HJT电池转换效率可高出0.5%~1%,电池片使用硅片厚度降低20%,银浆耗量降低20%,单瓦成本可降低10%, 保证产品技术在未来具有持续的领先性和更强的竞争力。
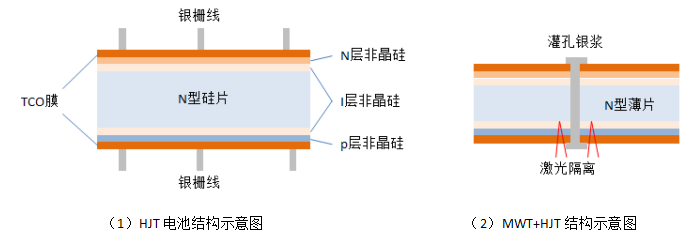
▲薄硅片,HJT与MWT“不谋而合”,挑战120μm极限
如图(1)和(2)所示,常规HJT异质结电池基本是一个对称结构,N型硅片两边有1-2nm的本征非晶硅隧穿钝化层,P型掺杂非晶硅作为发射极可以位于正面也可以位于背面,背面发射极更有利于降低正面膜层光的吸收和提升填充因子,所以逐渐成为量产HJT的首选。HJT电池因为其完美的表面钝化效果所以开路电压Voc不会随着硅片变薄而减少甚至还会提升,导致转换效率基本不随厚度减薄而改变,这就为超薄硅片的应用提供了可能,这也是降低主材硅成本最为有效和直接的方法。
根据测算,硅片厚度每降低10μm,单片硅片成本将降低3%~5%,这个对于价格高昂的N型硅片极为重要,但是薄片化带来的挑战也非常大,常规的焊带高温焊接的方式严重制约了硅片厚度的持续下降,所以目前量产最多只能降低到160μm左右,进一步的硅片减薄必须采用更先进的无应力互联封装方式,而MWT技术恰恰提供了完美的解决方案。所以HJT+MWT电池采用120μm甚至更薄的超薄硅片,只需要增加激光开孔和隔离工序即可。其工艺流程如下图所示:
●大尺寸超高效MWT+HJT电池工艺流程:
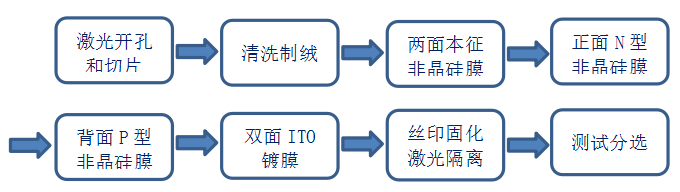
●MWT+HJT电池封装成组件工艺流程:
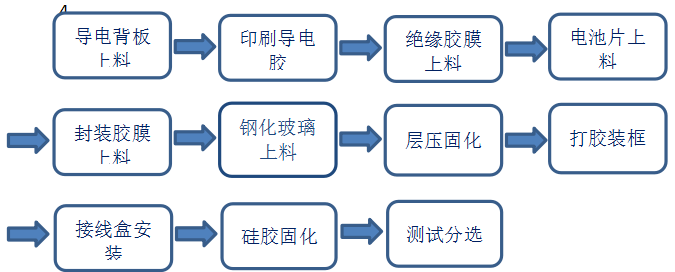
HJT电池使用的是低温银浆,常规的高温焊接工艺并不适合HJT电池的组件封装,所以HJT电池的封装至今仍然是行业面临的一个难题和痛点,而日托光伏的背接触MWT技术,在组件端采用的是“导电背板+导电胶”的先进二维封装方案,可以完美的解决HJT电池封装的问题。这种平面二维的无应力封装方式来源于SMT电子封装行业,日托光伏通过持续专注的研发投入,将其成功应用于MWT电池封装并实现产业化,采用该技术方案,可以完全消除常规电池封装中焊带的应用和高温焊接的过程。
消除了焊带及焊接过程产生的应力,导电胶低温固化工艺和电池片低温银浆的电极也完美贴合,并且支撑超薄的硅片应用(<120μm)和浆料耗量的降低(不需要长的银主栅线),同时降低了封装损失,提升了组件的耐候性和可靠性。
低成本,MWT+HJT成本测算
按照目前主辅材的价格,对比常规HJT电池和MWT+HJT电池的生产成本,基于G12大尺寸硅片,常规HJT电池采用的是160μm厚度N型单晶硅片,而MWT+HJT电池只需要120μm厚度的超薄硅片,有效降低电池片成本。此外基于MWT技术的无主栅设计,不仅可降低遮光损失,提升电池效率,还可节省20%的银浆耗量。

表1:MWT+HJT电池组件和常规HJT电池组件成本测算对比
如上表所示,相比较G12大尺寸常规HJT单晶电池,同尺寸的MWT+HJT电池量产效率要高出0.5%(绝对值),由于采取了超薄的120μm硅片,大幅降低了硅成本15%左右,加上MWT技术的低银浆耗量优势,MWT+HJT电池的单瓦成本可以比未来主流HJT电池低0.15元/W左右。在组件端,由于电池效率优势相同面积功率高出2%左右,也就是同样尺寸的组件额定功率要高出10W左右,结合电池片的单瓦成本优势,在组件端单瓦成本相对于常规HJT产品依旧有0.15元的低成本优势,这个单瓦成本甚至低于市场常规PERC+产品,但电池和组件转换效率要远远高于市场常规PERC+产品。
MWT+HJT技术的叠加,充分发挥了各自技术优势,并且解决了HJT技术产业化的“痛点”,进一步提效的同时大幅降低了生产成本,可以说MWT+HJT是“超高效”和“低成本”的极致组合,互相成就的最好伙伴。